Multi-Stage Wastegate Control Bleed Using
The EEPC
Description
This page
describes how to install a multi-stage wastegate control bleeds (WCBs)
setup using the Electronic Engine Performance Controller
(EEPC). To read more about WCBs, see the Increasing
Boost With Wastegate Control Bleeds page.
This setup gives you multiple stages of boost, depending on throttle position.
It also has an output for the Boost Peak Suppression, which uses the MAP
sensor to measure pressure. The particular example implements 3 stages
of boost.
Building
The EEPC
In order
for this system to work, you need to build the Electronic Engine Performance
Controller for it. The following page contains all the information
you need to do this:
EEPC:
TPS-Based WCB Controller With Boost Peak Supression
Be
sure to read all of the information on that page and to follow all the
testing and calibration procedures before installation. In addition
to the parts needed by the EEPC, you will also need the following parts
for the 3-stage setup:
-
(3) needle
valves of some type - see the Increasing Boost With
Wastegate Control Bleeds page
-
(3) vacuum
solenoids - best place to these is a salvage yard
-
(3) check
valves - another salvage yard or a MotorMite part
-
some 5/32"
I.D. vacuum hose, length depends on your application
-
some 18
guage or thicker wire - length depends on installation, multi-color is
always helpful
-
(3) plastic
"T" fittings for 3/16" I.D. hose
-
(1) restrictor,
possibly a second
-
maybe
- (1) 3/16" to 1/4" vacuum hose adapter with a short piece of 1/4" (7/32")
vacuum hose if needed for your wastegate actuator
Installation
How you
physically install the solenoids and needle valves is entirely up to you.
One important thing to remember is that the needle valve that is to be
set to the highest boost should have the shortest vacuum line path.
As you will see in the diagram below, the high boost valve goes through
the shortest part of only one solenoid, while the low boost valve goes
through the long parts of two solenoids. It is important to remember
this if you want a system that has good response. If you are going
to add more stages, just make sure the valve stages are lower and lower
as you go down the chain of solenoids. Also, the vacuum hose between
the boost peak suppression solenoid and the wastegate actuator should be
kept as short as possible. Try to mount this solenoid on the firewall
and/or near the brake booster.
The
optional restrictor or needle valve that is shown is to regulate the effect
of the boost peak suppression solenoid. When used with very responsive
turbochargers, such as the Mitsubishi TD04, the peak suppression solenoid
tends to knock the boost down way too far (about 5-7psi). Installing
a restrictor in the line feeding the normally closed barb of the solenoid
(not the common barb) will reduce the effect of the solenoid.
Getting the right size restrictor in there can be tricky, which is why
I recommend using a needle valve instead.
The
EEPC circuit provides the ground to the solenoids, so each solenoid needs
a common 12V source. It's always a good idea to put a small fuse
on this line, close to the power source. About a 3A fuse should work
well. It is best to install the EEPC inside the passenger compartment,
rather than under the hood. Even if you seal up the case well with
RTV, the extreme temperatures under the hood can cause the circuit to not
behave properly. Here is the diagram for the needle valve and solenoid
setup:
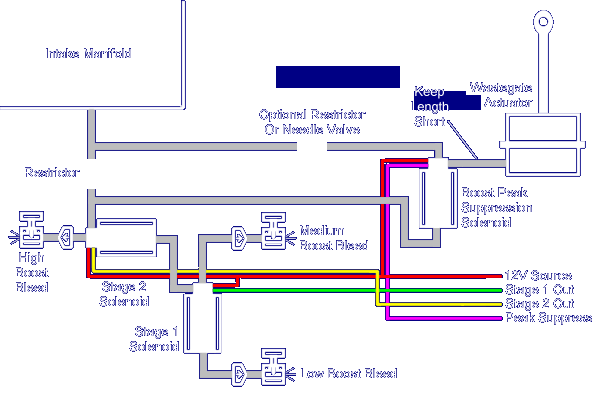
This EEPC needs the output
signal from the TPS and MAP
sensor. Please use your vehicle wiring diagram to locate these
wires. I highly recommend soldering into these wires, rather than
using wire splices. A reliable connection is very important.
If you have an 1987 or earlier vehicle, these wires are already available
in the passenger compartment in the harness to the logic module (see your
wiring diagram). For 1988 and later vehicles, the wires go right
from the engine to the 60-way connector on the SMEC or SBEC (see your wiring
diagram), which is next to the battery. You will have to run two
wires from under the hood back into the passenger compartment. The
EEPC will be wired like this:
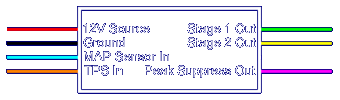
Calibration
To calibrate
this system, you need to think about how you want your system to respond.
The following procedure is a starting point and can be used as an example
if you wish to change your caliration later. The EEPC for this setup
actually has three TPS-controlled outputs for three solenoids. This
can potentially be used for 4 stages of boost, but this example has been
using 3 stages, so the 3rd output of the EEPC will not be used in this
setup.
As
far as I know the TPS for all of these
engines has an output voltage range of about 0V at closed throttle to 2.60V
- 3.00V at wide-open throttle (WOT). You can verify this by measuring
the voltage on the output of the sensor (the center wire) with the ignition
key in the "on" position. You must remember that the computer treats
WOT as a special condition. If you are not familiar with this, please
read the 2.2L/2.5L Turbo Engine Important Upgrade
Information page. Now you must choose the throttle positions
at which you want each stage to turn on. Below is a table showing
throttle position in degrees and the corresponding approximate TPS output
voltage:
Throttle Position
|
TPS Output
|
Closed Throttle
- 10 degrees
|
0V
|
20 degrees
|
0.38V
|
30 degrees
|
0.75V
|
Half Throttle
- 45 degrees
|
1.31V
|
60 degrees
|
1.86V
|
Computer
sees WOT - 79.3 degrees
|
2.60V
|
Actual WOT
(floored) - 90 degrees
|
3.00V
|
-
Set reference
voltage 1 of the EEPC (R1) to the point at which you want to go from low
to medium boost. Try about 1.30V (measure at pin 4 of U1), which
is about half throttle.
-
Set reference
voltage 2 (R2) to the point that you want to go from medium to high boost.
Try about 2.60V (measure at pin 6 of U1), which just at the beginning
of the WOT zone.
All MAP
sensors for our engines have an output voltage range of near 0V at full
vacuum to about 5V. The stock Chrysler MAP sensor for turbocharged
engines is a 2 bar sensor. Below is a table showing the manifold
pressure and its corresponding output voltage for the 2 bar MAP sensor.
The range shown is the reliable voltage output range of the sensor.
It can go higher than 4.90V, but the sensor manufacturer does not gauruntee
anything about it's output.
Manifold Pressure
(relative sea level / absolute)
|
2 Bar
MAP Output
|
14.31psi / 29.01psi
|
4.90V
|
14.00psi / 28.70psi
|
4.84V
|
13.00psi / 27.70psi
|
4.67V
|
12.00psi / 26.70psi
|
4.50V
|
11.00psi / 25.70psi
|
4.33V
|
10.00psi / 24.70psi
|
4.16V
|
9.00psi / 23.70psi
|
3.99V
|
8.00psi / 22.70psi
|
3.82V
|
6.00psi / 20.70psi
|
3.47V
|
4.00psi / 18.70psi
|
3.13V
|
2.00psi / 16.70psi
|
2.79V
|
0.00psi / 14.70psi
|
2.45V
|
5.00inHg / 12.24psi
|
2.03V
|
10.00inHg / 9.78psi
|
1.61V
|
15.00inHg / 7.33psi
|
1.19V
|
20.00inHg / 4.87psi
|
0.77V
|
25.00inHg / 2.41psi
|
0.35V
|
29.10inHg / 0.40psi
|
0.02V
|
-
Set reference
voltage 4 (R4) to your absolute maximum boost setting. This should
just above the setting of your high boost needle valve. If you adjust
it too close, you may get boost oscillation. If you have overboost
shutdown problems, then set it to be just below your overboost shutdown
voltage (typically around 4.9V).
Once you
have the unit installed and calibrated, take it out for a spin. You
can tweak your boost pressures and the boost stage references as you see
fit. Enjoy!
This page is maintained by
Russell W. Knize and was last updated 04/21/99. Comments? Questions? Email
minimopar@myrealbox.com.